How Approved Sheet Metal fabricated a complex laser enclosure that other metal fabricators refused to touch, all with quick-turn precision fabrication and exceptional engineering at an impressive price.
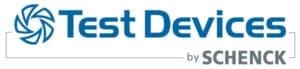
The Company
Test Devices offers the world’s most advanced and accurate spin testing equipment, services, and semi-finish machining services, delivering unparalleled safety and innovation to clients in the aerospace, aviation, power generation, energy storage, air handling, automotive, electronics, and medical devices industries.
A branch of SCHENCK USA, a company owned by Germany-headquartered global conglomerate The Dürr Group, Test Devices has provided engineering testing services for over 50 years.
Industry: Engineering Testing
Location: Hudson, Massachusetts
The Project
The Challenge:
As part of the US Air Force-sponsored program, Test Devices needed a guaranteed 100% light-tight enclosure for a laser system so powerful even brief exposure could cause blindness. The enclosure would also house Test Devices’ optical strain imaging system, which, in conjunction with the laser, would capture high-quality images of parts undergoing high-speed spin testing for complete surface strain mapping. The corners of the enclosure presented the biggest challenge, and many vendors had already refused the project, unwilling to attempt the epoxy seams.
The Solution:
Approved Sheet Metal collaborated closely with Test Devices to refine the enclosure’s design, leveraging 100 years of combined engineering experience to manufacture the complex, high-precision custom sheet metal enclosure.
The Outcome:
At the advice of the Approved Sheet Metal team, Test Devices repositioned some of the enclosure’s rivet holes and reduced the rivet count, improving the design’s functionality and reducing manufacturing costs. From project launch to completion, Approved Sheet Metal impressed Test Devices by delivering the completed enclosure within six weeks.
Seeking the Right Quick-Turn Manufacturing Partner for Laser Safety
Test Devices’ proposed enclosure required strict adherence to laser safety practices.
Though the entire system, once completed, would be considered a very safe Class 1 product, the laser was a Class 4, the most hazardous rating a laser can receive. So powerful it can cause materials to ignite, the Class 4 laser had to be completely enclosed in a light-tight box with epoxy seams that would protect people from serious injury.
During high-speed spin testing, the laser imaging system would capture displacements on a part’s surface, providing critical data for Test Devices’ customers to validate their analytical models.
Though the two companies hadn’t previously worked together, Test Devices was familiar with Approved Sheet Metal’s reputation for the high-quality manufacturing of large, complex assemblies.
“Quick-turn is what we do,” said Tim Koukos - engineer for Approved Sheet Metal—and it was ASM’s familiarity with the job’s complexities that won over the Test Devices team.
“Their responsiveness and lead time were quite impressive,” noted Test Devices’ Senior Mechanical Engineer Cameron DeWallace.
Collaborating with Approved Sheet Metal to Achieve Excellence
After reviewing the project requirements, drawings, and CAD models sent over by Test Devices, Approved Sheet Metal got to work helping the engineering testing team make Design for Manufacturing (DFM) improvements. “We had a lot of manual operations that were unnecessary,” explained Cameron, “and Approved Sheet Metal helped us streamline.”
Following numerous DFM modifications, the final design for the laser imaging system’s 44”x30”x31” enclosure incorporated 32 unique parts and a total of 82 pieces.
Approved Sheet Metal leveraged laser cutting, metal bending, and welding processes to fabricate the custom sheet metal product. To simplify the assembly process, ASM’s engineers added “slot and tab” connections on the assembly pieces, enabling a seamless fit and exceptional welding.
A thorough surface grind paired with powder coating and epoxy resulted in a smooth finish. Lastly, the shop’s professionals ensured light tightness with additional epoxy spot application.
“The goal was to make this project as easy and cost-effective as possible,” explained Tim, whose 43 years of engineering experience played a key role in ensuring an optimal outcome.
“The result was quite good,” acknowledged Cameron. “The enclosure that was delivered was exactly what we needed.”
Key Differentiators
Formed in 2020, Approved Sheet Metal was built by leaders in the sheet metal fabrication industry. They leverage technology to get parts quoted, fabricated, and delivered faster than anyone. They are dedicated to their craft and proud to be making parts in America.
Precision Prototype Sheet Metal from Conception to Completion
Approved Sheet Metal takes hand sketches, detailed prints, and CAD models requiring first article inspection to turn ideas into physical sheet metal parts. They understand how important it is to hit deadlines and are committed to supporting customers’ journeys from conception to completion.
Wide Range of Capabilities
Approved Sheet Metal has 30+ years of experience, 20,000+ sq. feet of manufacturing space, and state-of-the-art processes and equipment from quoting and programming to punching, forming, hardware insertion, welding, finishing, and inspection.
Quick Turnaround Time
Approved Sheet Metal responds to all quotes within 4 hours and turns around rapid prototypes in record time. They also have a same-day rush service for flat sheet metal parts.
Precision Fabrication Services to Meet Exacting Specifications
In fact, the project went so well that Test Devices quickly followed up by sending more designs to Approved Sheet Metal for engineering assistance and production solutions—both ongoing needs for this customer. Along with customizing engineering test machines for clients worldwide, Test Devices also offers multiple highly specialized solutions:
- A complete range of turnkey spin rigs for proof (burst) testing targeted at R&D applications
- Over-speed (pre-spin) testing for production requirements
- Semi-finish machining services
- Subscale Jet Engine Testing
“We got a quote and placed a PO within the same day!” Cameron said. “Approved Sheet Metal’s communication and the speed at which they’re able to get stuff done is exactly what we need.”
We Don’t Just Get It, We Get It Done™
“The experience of working with Approved Sheet Metal was very much above average—even when compared to working with other shops in general,” Cameron expressed when the laser enclosure project had been completed. “I think the quality, experience, and communication are definitely top-notch.”
Hiro Endo, Test Devices’ Chief Technology Officer, was also delighted with the outcome. “I’ve worked with a lot of precision fabrication shops before and didn’t have a good experience,” he said. “A lot of sheet metal products come out with gaps or bent in a funny way. When I saw Approved Sheet Metal’s workmanship on the enclosure, I was impressed that [they] put it together without any gaps!”