Last updated on January 13th, 2025 at 09:13 am
Surface finish is an essential consideration for many sheet metal fabrication projects—including, most commonly, parts requiring beautiful cosmetic appearances and pharmaceutical or medical-grade parts that need to perform in clean environments.
Today, we’ll take a closer look at different surface finishing scales as well as surface finish considerations to ensure you get the exact parts you need.
Table of Contents
- 1 Surface Finish Scales for Sheet Metal Fabricated Parts
- 2 Creating Beautiful Surface Finishes for Sheet Metal Fabricated Parts
- 3 Surface Finish Considerations for Sheet Metal Fabricated Parts
- 4 Recommended Default Sheet Metal Tolerances
- 5 Sheet Metal Surface Finish FAQ
- 5.0.1 What is surface finish, and why is it important in sheet metal fabrication?
- 5.0.2 What are some commonly used surface finish scales for sheet metal fabricated parts?
- 5.0.3 How can I achieve the best surface finish for my sheet metal fabricated parts?
- 5.0.4 What should I consider before specifying surface finish requirements for my sheet metal fabricated parts?
- 5.0.5 How does Approved Sheet Metal ensure that my sheet metal fabricated parts meet my surface finish requirements?
Surface Finish Scales for Sheet Metal Fabricated Parts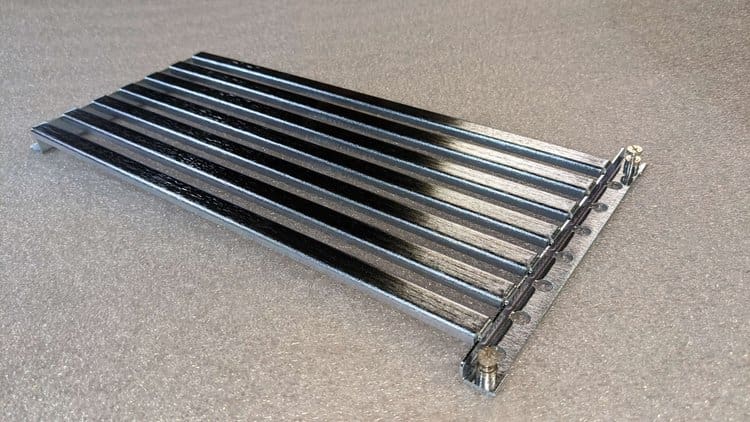
There are several different ways to measure the surface finishes of sheet metal fabricated parts.
Fabricators, machinists, and metal finishers often use the highly technical Ra (Roughness Average) scale, which measures the average surface heights and depths across a surface. The problem is that maintaining a specific Ra value is difficult at a microscopic level for sheet metal fabricated parts—and it isn’t essential for many sheet metal applications.
An alternative method is to indicate the grit—the number of scratches per linear inch of abrasive pad—that should be used to finish a part. Higher grit values indicate smoother surface finishes. This is one of the more common ways that sheet metal fabricators and customers communicate about surface finish requirements.
However, the easiest and best way to specify surface requirements for sheet metal fabricated parts is to use the preferred scale for the source material. For example, we would use this simple scale for stainless steel:
- 2B: Bright, Cold Rolled
- 3: Brushed, 120 Grit
- 4: Brushed, 150 Grit
- 8: Mirror
- BA: Bright Annealed
Creating Beautiful Surface Finishes for Sheet Metal Fabricated Parts
To achieve the best surface finish possible for sheet metal fabricated parts, we recommend sourcing a material that already has a surface finish comparable to the desired finish.Then, we can use one of these standard methods to clean it up even further:
- Employing our Timesaver Abrasive Belt Finishing Machine to clean up the surfaces of sheet metal fabricated parts and get them to spec. This machine is capable of deburring, edge rounding, finishing, laser oxide, and heavy slag removal.
- Using successively finer belts and compounds to achieve a near mirror finish—although this type of finish typically isn’t required for sheet metal fabricated parts.
Surface Finish Considerations for Sheet Metal Fabricated Parts
Consider these factors before specifying surface finish requirements for your sheet metal fabricated parts:
- A higher surface finish doesn’t necessarily result in a better aesthetic appearance. Surface finishes with exceptionally low Ra values lose some of their grain, which can compromise the appearance of the finish in certain cases.
- The smoothest surfaces aren’t always ideal for painting and powder coating. If you plan to have your sheet metal part painted or powder-coated, we recommend leaving some texture on the surface. When the surface is too smooth, these additional finishing operations will highlight any scratches or imperfections. A slightly textured surface yields a more uniform appearance.
- Achieving an exceptionally smooth surface finish adds cost and time to a project. You can save time and money by minimizing surface finish operations on sheet metal fabricated parts. You may consider this option for sheet metal prototypes or internal parts that don’t need to be aesthetically perfect.
Industry-Specific Applications
Surface finishes in sheet metal fabrication play a crucial role across various industries, with each sector having unique requirements based on the applications of their products. Below are some examples of industry-specific applications where surface finish is critical:
1. Medical and Pharmaceutical Industries
- Key Requirements: High-grade finishes like 2B or mirror finishes to ensure cleanliness, prevent contamination, and maintain sterility.
- Applications: Surgical instruments, medical device enclosures, and cleanroom equipment.
- Standards: Must often comply with regulations such as ISO 13485 or FDA standards for materials used in healthcare.
2. Food and Beverage Industry
- Key Requirements: Smooth, non-porous finishes (e.g., 2B or BA) that prevent bacteria growth and are easy to clean.
- Applications: Stainless steel tanks, food processing machinery, and kitchen equipment.
- Standards: Surface finishes must meet NSF and USDA guidelines for food safety.
3. Aerospace Industry
- Key Requirements: Lightweight parts with corrosion-resistant finishes that ensure durability in extreme conditions.
- Applications: Aircraft panels, turbine blades, and structural components.
- Standards: Often require adherence to AS9100 and specific roughness average (Ra) values.
4. Electronics and Semiconductors
- Key Requirements: Highly precise finishes to minimize electromagnetic interference (EMI) and ensure proper electrical conductivity.
- Applications: Enclosures for sensitive electronics, heat sinks, and semiconductor manufacturing equipment.
5. Automotive Industry
- Key Requirements: Aesthetic finishes for visible parts, and durable, corrosion-resistant finishes for functional components.
- Applications: Car exteriors, interior panels, and engine components.
- Standards: Surface finishes must often meet durability and appearance benchmarks set by manufacturers.
Surface Finish vs. Functionality
Surface finishes not only enhance the aesthetic appeal of sheet metal parts but also play a critical role in their functionality. Below are some ways surface finish directly impacts a part's performance:
1. Corrosion Resistance
- A smoother surface finish, such as a mirror or BA finish, minimizes crevices where moisture or chemicals can accumulate, reducing the likelihood of corrosion.
- Industries like marine and food processing often require these finishes for longevity in corrosive environments.
2. Friction and Wear Resistance
- Components requiring low friction, such as sliding parts in machinery, benefit from polished or DA sanded finishes to minimize wear and extend the lifespan of the parts.
3. Adhesion for Coatings
- A slightly textured surface finish, such as one achieved with grit blasting, improves the adhesion of paints, powder coating, or adhesive films. Conversely, overly smooth surfaces can lead to peeling or flaking.
4. Thermal and Electrical Conductivity
- Highly polished surfaces ensure better conductivity in electrical and thermal applications, such as heat sinks or electronic enclosures.
5. Cleanability and Hygiene
- In industries like healthcare and food processing, smoother finishes reduce contamination risks and make surfaces easier to clean, maintaining hygiene standards.
6. Structural Integrity
- Excessively rough finishes can create stress concentrations, leading to cracks or failures under load. Specifying an appropriate surface finish can enhance durability and reliability.
At Approved Sheet Metal, we’re committed to delivering sheet metal fabricated parts that meet customers’ specifications and will always do what it takes to achieve the surface finish you desire. Our attention to detail and obsession with quality is second to none. Request a quote today, and we’ll respond ASAP!
Sheet Metal Surface Finish FAQ
Surface finish refers to the texture or smoothness of a metal surface after it has been fabricated. It is essential in sheet metal fabrication because it affects the part's appearance, performance, and compatibility with additional finishing operations like painting and powder coating.
The Ra (Roughness Average) scale and the grit scale are commonly used to measure the surface finishes of sheet metal fabricated parts. The preferred scale for the source material is also used to specify surface requirements for sheet metal fabricated parts.
To achieve the best surface finish, you should source a material that already has a surface finish comparable to the desired finish. Then, you can use standard methods like employing an abrasive belt finishing machine or using successively finer belts and compounds.
Before specifying surface finish requirements, you should consider factors like the part's aesthetic appearance, compatibility with additional finishing operations like painting and powder coating, and cost and time constraints.
Approved Sheet Metal is committed to delivering sheet metal fabricated parts that meet customers' specifications and will do what it takes to achieve the desired surface finish. Their attention to detail and quality is second to none, and they offer a quote response ASAP.