Last updated on February 23rd, 2024 at 08:47 am
Customers in the medical device industry have long trusted Approved Sheet Metal to fabricate chassis, covers, custom medical carts, enclosures, and more.
Now, thanks to our recent acquisition of Nashua Fabrication, we’re adding a new capability that will allow us to support the medical device industry like never before: we’re fabricating cleanroom-grade custom stainless steel tubular frames! Applications for these frames include supply carts, trays, chassis, test tube racks, and baskets.
Table of Contents
- 1 Considerations for Cleanroom Grade Stainless Steel Tubular Frames
- 2 Why Choose Approved Sheet Metal for Cleanroom Grade Stainless Steel Tubular Frames?
- 3 Recommended Default Sheet Metal Tolerances
- 4 Tubular Frames FAQ
- 4.0.1 Why is stainless steel the preferred material for cleanroom-grade tubular frames in medical and pharmaceutical applications?
- 4.0.2 How does Approved Sheet Metal ensure the precision and accuracy of its cleanroom-grade stainless steel tubular frames?
- 4.0.3 Can Approved Sheet Metal assist with the design phase of tubular frames, or do they only provide fabrication services?
- 4.0.4 What types of finishes or coatings are available for tubular frames fabricated by Approved Sheet Metal?
- 4.0.5 What is the typical lead time for the fabrication of cleanroom-grade stainless steel tubular frames at Approved Sheet Metal?
Considerations for Cleanroom Grade Stainless Steel Tubular Frames
When it comes to medical devices and equipment, cleanliness and safety are of paramount importance. These high standards apply not only to tools that come into direct contact with a person's body but also for any devices and equipment in a hospital or clinic setting.
To uphold cleanroom-grade standards for medical and pharmaceutical applications, we most often use stainless steel, the go-to material for custom sheet metal medical devices and equipment.
Stainless steel is ideal for medical applications due to its:
- High corrosion resistance. While thermoplastic polymers will degrade past 300°F (~148.9°C), stainless steel can withstand the high heat and harsh chemicals used in medical sterilization processes without distorting. Due to the small amount of molybdenum in its blend, 316 stainless steel specifically can withstand phosphoric acids and chlorine solutions used in high-standard cleaning.
- Built-in polished surface. Stainless steel’s inherent smoothness makes it an ideal surface for applications that need to be sterile at all times. It doesn’t require any extra coatings that could eventually flake off and cause contamination. And there are no crevices where dirt or bacteria can hide.
- Formability. Stainless steel also offers high formability for precision sheet metal applications. The addition of selenium and sulfur in stainless steel blends makes the material easier to machine, especially for smaller components requiring tight tolerances.
- Strength. Stainless steel packs a minimum strength of 75,000 psi. Our tubular frames are heavy-duty enough to carry bulky medical equipment without compromising the integrity of the structure.
Why Choose Approved Sheet Metal for Cleanroom Grade Stainless Steel Tubular Frames?
Many sheet metal fabrication shops can cut and drill metal, weld it together, and polish it. But not every fabrication company has the steady hands, talent, and experience that we have. Simply put, we’ve got skills—and that’s something you can’t buy with a shiny new piece of technology.
Here’s what sets our team apart from the competition:
Digital processes combined with beautiful craftsmanship.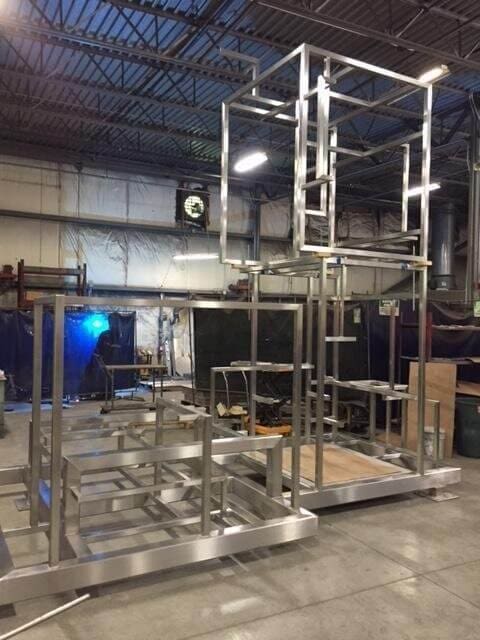
We’re high-tech with many of our processes, but old school on the shop floor.
For example, we use advanced programs like SOLIDWORKS to mimic how joints will interact in a weldment, allowing our team to adjust dimensions as necessary. This software also calculates for weld gaps, as well as the amount of steel expansion when heat is applied during full penetration welds.
But once we’re on the shop floor, we use no special equipment—just superior skill that results in beautiful craftsmanship. We prepare and fixture tubular stainless steel with the highest degree of care and attention to ensure accuracy and precision for every part.
Experienced welders.
We’ve got a team of master welders with 20+ years of experience. You simply can’t acquire their level of talent except by plying your trade for decades. Our team’s skills have been forged over time in hundreds of practical applications.
Our welders use a special technique to compensate and accommodate for the amount of heat a piece sheet metal will sustain. First, they unbend the material so they have a good feel for how much the metal will move once heat is applied. Then, they deliberately cut the metal a bit bigger than required so it’ll still be the right size after welding.
They also use a special technique for T-joints, providing stability for a part by anticipating where the material will move and securely bracing it in the opposite direction.
Superior polishing capabilities.
We understand that polishing is critical for medical devices and equipment because smooth surfaces are easier to clean and debris is less likely to accumulate when there are no crevices or grooves.
At our metal fabrication shop, we do all polishing with custom-made hand tools. Working with hand tools takes years of expertise and an incredible steadiness. We’re proud to say that our polishing team consistently produces impeccably finished parts and assemblies.
Whether you need medical equipment or a custom sheet metal fabrication for an entirely different industry, you can rely on Approved Sheet Metal for precision fabrication.
We work with many materials in addition to stainless steel, and we can meet strict requirements in industries that demand exact specifications, such as aerospace, communications, and many more.
Request a quote for your next custom sheet metal fabrication!
P.S. Want to learn the skills of the trade? If you’re interested in learning from the masters, join our awesome team!
Tubular Frames FAQ
Stainless steel is the preferred material for cleanroom-grade tubular frames in medical and pharmaceutical applications due to its high corrosion resistance, built-in polished surface that ensures sterility, formability for precision machining, and impressive strength, with a minimum strength of 75,000 psi.
Approved Sheet Metal ensures precision and accuracy through a combination of advanced digital processes and skilled craftsmanship. We use software like SOLIDWORKS for precise planning, and our experienced welders employ techniques to compensate for material movement during welding. We also perform meticulous polishing using custom-made hand tools.
Approved Sheet Metal offers comprehensive services that include not only fabrication but also assistance with the design phase. Our team can work collaboratively with customers to develop custom tubular frame designs that meet specific requirements and standards. Whether you have a design in mind or need assistance from the conceptual stage, we can provide expert guidance and support throughout the process.
Approved Sheet Metal can provide various finishes and coatings for tubular frames to meet specific aesthetic or functional requirements. This may include powder coating, painting, or specialized finishes for corrosion resistance. The choice of finish can depend on your project's needs, and our team can offer guidance on selecting the most suitable option for your application.
The lead time for the fabrication of cleanroom-grade stainless steel tubular frames at Approved Sheet Metal can vary depending on factors such as project complexity and volume. It's recommended to contact our team directly for a project-specific lead time estimate, as they strive to meet individual customer needs efficiently.