Last updated on April 2nd, 2025 at 09:40 am
You may or may not be aware that PEM® recently stopped producing their TD™ line of self-clinching cable tie-mounts, TY-D® and TD™, and switched to a TDS™ product line in June 2022.
While some suppliers still have TD hardware on their shelves, inventory is dropping quickly. Many precision sheet metal shops, including Approved Sheet Metal, are working to secure TDS™ products as a replacement.
The change might seem minor, but there are implications for customers and suppliers alike. As your trusted partner for rapid sheet metal services, we’re committed to making this transition as seamless as possible for our customers.
Here’s what you need to know.
Table of Contents
- 1 What Are TD and TDS Cable Tie-Mounts?
- 2 What Types of Hardware Are Changing?
- 3 Update Designs to Include TDS Hardware for Fast Quoting
- 4 Design & Specification Best Practices
- 5 Sheet Metal Hardware Hole Sizes Chart
- 6 PEM® TD™ Hardware Changes – Steel to Stainless Steel FAQ
- 6.0.1 What is the difference between TD and TDS Cable Tie-Mounts?
- 6.0.2 What benefits do TD and TDS Cable Tie-Mounts offer?
- 6.0.3 Which TD hardware types are being phased out, and what are their replacements?
- 6.0.4 Why should customers update their designs to include TDS hardware?
- 6.0.5 Is there a supply chain issue affecting TDS hardware availability?
What Are TD and TDS Cable Tie-Mounts?
TD and TDS hardware are two versions of the same product suite of self-clinching cable tie-mounts (also known as tie-downs) that provide a secure attachment point when mounting wires to electronic enclosures or chassis. The tie-downs are a vast improvement over other mounting methods such as zip-ties and come with many benefits:
- Installation is quick and permanent without requiring any screws or adhesives that can fail over time
- Tie-downs won’t protrude on an assembly’s opposite side, enabling panels to lie flush
- The fasteners ensure wires maintain their proper placement and are durable enough to function properly for the lifetime of an assembly
While TD and TDS hardware are the same from a functional and dimensional perspective, the materials are different: TD hardware was made from sintered steel, and TDS hardware is made from stainless steel. We expect the material change to make TDS hardware stronger.
The transition to stainless steel will also allow us to install TDS products before assemblies undergo finishing treatments such as chromate, which wasn’t a possibility with TD hardware.
What Types of Hardware Are Changing?
Five types of TD hardware are being phased out as part of this change:
- TD-175-12X
- TD-175-12ZI
- TD-40-4ZI
- TD-60-4ZI
- TD-60-6ZI
However, the good news is that six TDS versions are being produced as 1:1 replacements:
- TDS-175-12
- TDS-175-12ZI
- TDS-40-4
- TDS-40-4ZI
- TDS-60-6
- TDS-60-6ZI
Update Designs to Include TDS Hardware for Fast Quoting
We encourage our customers to update their designs to include TDS hardware so that all documentation is correct and we can deliver a fast quote. Want us to handle the updates for you? No problem! We can update any designs we receive with TD hardware callouts with the appropriate replacement TDS products.
Industry rumors indicate that increased demand for TDS products has put massive pressure on the supply chain, with some shops waiting months before getting their hands on the new line of hardware.
If TDS hardware isn’t available for your part, we’ll do what we always do at Approved Sheet Metal-proactively communicate with our customers and do whatever it takes to find a solution.
You can count on us to know about pertinent industry information (including, but not limited to, hardware updates!) so you don’t have to. We’re happy to take care of all the seemingly small but essential details for our sheet metal fabrication customers.
Design & Specification Best Practices
As the transition from TD™ to TDS™ hardware takes effect, updating design files and engineering specifications is critical to ensuring seamless integration into production. Below are key best practices for specifying and designing with TDS hardware in sheet metal assemblies.
1. Update CAD Models and Engineering Drawings
- Revise part numbers: Ensure all CAD models, drawings, and BOMs reflect the new TDS hardware part numbers instead of obsolete TD components.
- Adjust callouts: Clearly specify “TDS” hardware in engineering drawings to avoid misinterpretation or supply chain issues.
- Check tolerance requirements: While TDS hardware maintains the same dimensional specifications as TD, always confirm that hole sizes and installation tolerances match manufacturer recommendations.
2. Consider Material Compatibility
- Panel Hardness Limitations: Self-clinching fasteners require the base material to be softer than the hardware itself. Stainless steel fasteners like TDS hardware require aluminum or mild steel panels for proper installation. If using harder materials, consider alternative fastening methods.
- Electrochemical Corrosion Risks: When pairing stainless steel TDS hardware with aluminum panels, galvanic corrosion may occur over time. Applying an isolating coating or using stainless steel panels can help mitigate this risk.
3. Factor in Finishing & Coating Adjustments
- Pre-finishing installation: Unlike TD hardware, which required installation after finishing due to corrosion concerns, TDS hardware can be installed before chromate conversion coatings or anodizing. This simplifies the manufacturing process and reduces lead time.
- Powder Coating & Paint Masking: Since TDS hardware is stainless steel, it may require masking or pre-treatment for optimal paint adhesion. Ensure that masking requirements are documented in production notes.
4. Verify Load & Environmental Requirements
- Weight and Strength Considerations: While stainless steel offers improved corrosion resistance, it may have different load-bearing properties than sintered steel. Verify that TDS hardware meets application-specific mechanical requirements.
- Temperature & Humidity Effects: If the assembly operates in extreme temperatures or humid environments, consider testing the long-term durability of TDS hardware under those conditions.
5. Ensure Fastener Availability in Procurement Plans
- Lead Time Adjustments: Due to increased demand, TDS hardware may have longer procurement lead times. Work closely with your supplier to avoid production delays.
- Alternative Sourcing Options: If TDS hardware is unavailable, evaluate whether other self-clinching cable tie mounts from different manufacturers can serve as drop-in replacements.
By implementing these best practices, engineering teams can optimize their designs for the TDS transition while ensuring manufacturability, reliability, and cost-effectiveness. If you need assistance updating your designs, our team at Approved Sheet Metal is happy to help!
Sheet Metal Hardware Hole Sizes Chart
CHART DOWNLOAD
Hardware hole sizes are the number one thing sheet metal fabricators have to fix before sending a part to the floor. So we have created a referenceable chart for product developers that are designing sheet metal parts. Use this chart to find the correct hole size for the hardware you select.
Get it now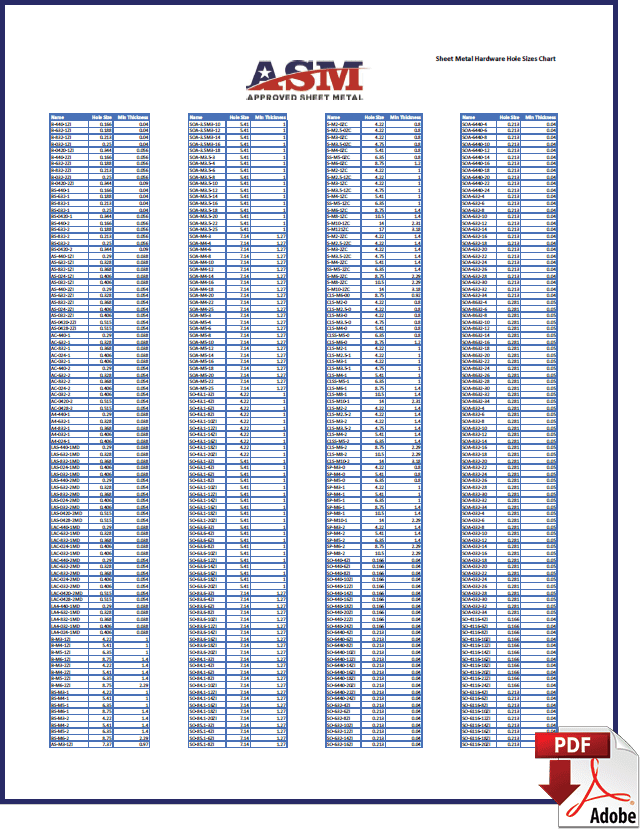
PEM® TD™ Hardware Changes – Steel to Stainless Steel FAQ
What is the difference between TD and TDS Cable Tie-Mounts?
TD and TDS Cable Tie-Mounts are two versions of self-clinching cable tie-mounts that provide a secure attachment point for mounting wires to electronic enclosures or chassis. While they serve the same function, the main difference is that TD hardware is made from sintered steel, while TDS hardware is made from stainless steel, making TDS stronger and allowing for installation before finishing treatments.
What benefits do TD and TDS Cable Tie-Mounts offer?
TD and TDS Cable Tie-Mounts offer several benefits, including quick and permanent installation without screws or adhesives, flush panel mounting, and ensuring proper wire placement. They are durable and reliable throughout the lifetime of an assembly.
Which TD hardware types are being phased out, and what are their replacements?
Five TD hardware types are being phased out: TD-175-12X, TD-175-12ZI, TD-40-4ZI, TD-60-4ZI, and TD-60-6ZI. They are being replaced with six 1:1 replacements: TDS-175-12, TDS-175-12ZI, TDS-40-4, TDS-40-4ZI, TDS-60-6, and TDS-60-6ZI.
Why should customers update their designs to include TDS hardware?
We encourage customers to update their designs with TDS hardware to ensure accurate documentation and expedite the quoting process. We can assist with updating designs that originally called for TD hardware to specify the appropriate TDS replacements.
Is there a supply chain issue affecting TDS hardware availability?
Yes, industry rumors suggest increased demand for TDS products has put pressure on the supply chain, leading to delays. However, Approved Sheet Metal is committed to proactive communication with customers and finding solutions if TDS hardware isn’t immediately available, ensuring a seamless transition for our customers.