Last updated on January 2nd, 2025 at 01:56 pm
If you’re accustomed to selecting 6061-T6 aluminum for machining, you may find yourself automatically requesting that same material for your sheet metal parts. But 6061 aluminum isn’t typically the best choice for a sheet metal part. For aluminum fabrication, we usually recommend 5052-H32 instead.
Here, we’ll outline the differences between 6061 and 5052 and explain why 5052 is the superior choice for sheet metal fabrication.
Table of Contents
- 1 Key Differences Between 6061-T6 vs. 5052-H32 Aluminum
- 2 Custom Aluminum Fabrication at Approved Sheet Metal
- 3 Sheet Metal Design for Manufacturing
- 4 5052-H32 Versus 6061-T6 for Sheet Metal Fabrication FAQ
- 4.0.1 What are the key differences between 6061-T6 and 5052-H32 aluminum for sheet metal fabrication?
- 4.0.2 Why is 5052-H32 preferred over 6061-T6 for fabricated parts?
- 4.0.3 What are the primary considerations when choosing between 6061-T6 and 5052-H32 for aluminum fabrication?
- 4.0.4 Are there specific applications where 6061-T6 or 5052-H32 excel over the other?
- 4.0.5 What should be done when 6061-T6 is the specified material but concerns exist about its fabrication suitability?
Key Differences Between 6061-T6 vs. 5052-H32 Aluminum
While both aluminum alloys are lightweight, strong, corrosion-resistant, and weldable (with some potential for heat deformation), the two materials are not interchangeable.
Choose 6061-T6 for machined parts
6061-T6 aluminum is heat-treated and very hard, so it machines beautifully!
However, 6061 does not play well with forming processes, as the alloy is highly likely to crack when formed to 90 degrees or beyond. If you must have a 6061 aluminum part with a 90-degree bend, we recommend making the internal radii equal to at least 2x to 3x the material thickness.
Cosmetic issues such as scratches and dents are also considerations when using 6061-T6 for aluminum fabrication. These cosmetic concerns can be managed, but be aware that fixing surface blemishes may increase both cost and lead time.
The properties of 6061-T6 aluminum include:
- Yield strength: 241 MPa (35,000 psi)
- Ultimate tensile strength: 290 MPa (42,000 psi)
- Primary alloying elements: magnesium and silicon
Common applications for 6061-T6 include:
- Aerospace
- Aircraft
- Bridges
- Rivets
- Train cars
- Towers
- Transportation operations
- Vehicle frames
Choose 5052-H32 for fabricated parts
Because 5052-H32 aluminum is not heat-treated, it embodies high fatigue strength and elasticity, making it ideal for forming. Approved Sheet Metal provides crack-free aluminum fabrication for high-quality 5052 sheet metal parts with surprisingly smooth surface finishes.
And at approximately $2 less per pound than 6061 aluminum, 5052-H32 makes more sense for your fabricated parts based on price alone!
The properties of 5052-H32 aluminum include:
- Yield strength: 193 MPa (28,000 psi)
- Ultimate tensile strength: 228 MPa (33,000 psi)
- Primary alloying elements: magnesium and chromium
Common applications for 5052-H32 include:
- Panels
- Brackets
- Enclosures
- Weldments
- Marine equipment
- Medical devices
- Assemblies
Custom Aluminum Fabrication at Approved Sheet Metal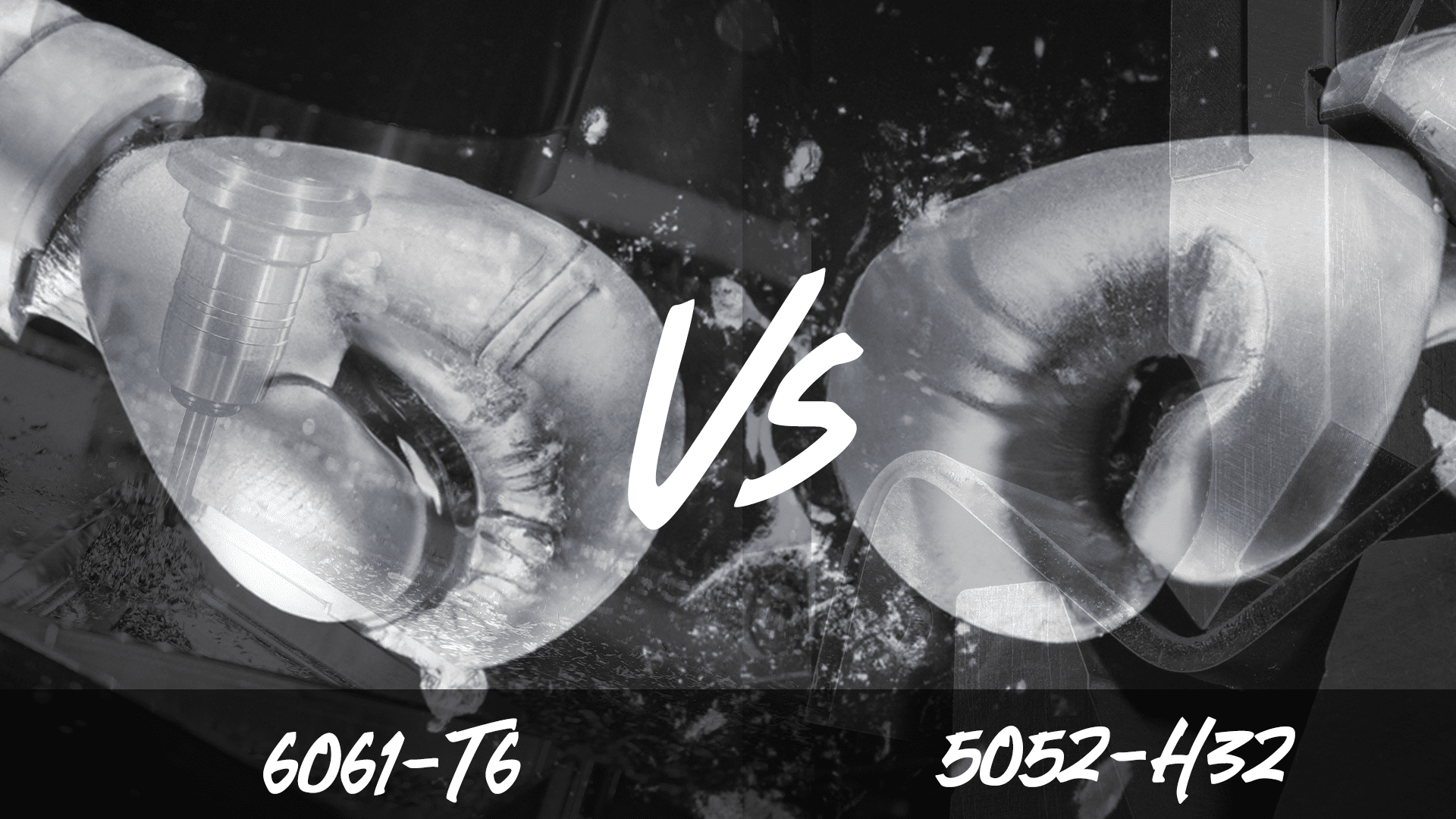
Our customers often request 6061-T6 aluminum for enclosures or boxes with lids—a totally reasonable material callout. Yet when the customer’s design specifies tight radii, we’ll almost always recommend a material swap to 5052-H32 aluminum. The cracking and breaking risks posed by 6061 frequently makes 5052 a significantly better choice, and we will highlight this substitution as an exception in your quote.
When you need to see for yourself…
We get it: engineers and buyers are visual learners. So please don’t hesitate to contact us to discuss a material swap we’ve recommended for your project. We’re happy to show you examples of parts formed from both aluminum alloys. You’ll be able to see for yourself how 6061-T6 can crack during aluminum fabrication.
Even when reviewing a simple 90-degree bracket design for 6061-T6 fabrication, we almost always recommend a material swap to 5052-H32 so we can ensure optimum quality and prevent potentially costly complications.
When you’ve read that 6061-T6 is “easy to form…”
A quick online search will surface articles suggesting that 6061 aluminum is easily fabricated—and it’s true that aluminum fabrication with 6061 is possible! To ensure the material holds up to the forming process, however, additional considerations invariably apply.
We may need you to increase the internal bend radii, or it may be necessary to begin with a T0 temper and then heat-treat the finished part. No matter how we’ll need to prep your 6061 material, you should anticipate a longer lead time and additional costs.
Common Challenges in Aluminum Sheet Metal Fabrication and How to Overcome Them
Aluminum sheet metal fabrication offers a range of benefits, but like any manufacturing process, it comes with its own set of challenges. Understanding these challenges and knowing how to overcome them can help ensure that the final product meets your expectations in terms of quality, performance, and cost. Below, we’ve outlined some of the most common issues faced during aluminum fabrication and the best practices to overcome them.
1. Cracking During Forming
One of the most common challenges when working with aluminum alloys, especially 6061-T6, is cracking during the forming process. Aluminum is susceptible to cracking when it’s bent or stretched beyond its elastic limit. This is particularly true for materials that are heat-treated or hardened.
How to Overcome It:
- Choose the right alloy: For parts requiring heavy forming, like tight bends, consider using 5052-H32, which has better formability and fatigue resistance compared to alloys like 6061.
- Increase bend radii: For alloys prone to cracking, such as 6061-T6, increase the internal bend radii to at least 2x to 3x the material thickness. This helps to prevent cracks at the corners.
- Annealing: If you must work with a hardened alloy like 6061-T6, you can anneal the material to soften it before forming and then reheat treat it after fabrication.
2. Surface Scratches and Dents
Aluminum, especially alloys like 6061-T6, can be easily scratched or dented during handling, machining, or transportation. These cosmetic issues can be a concern if your project demands a high-quality, aesthetic finish.
How to Overcome It:
- Handle with care: Implement better handling practices, such as using soft, protective materials (e.g., foam or felt) during transport and storage.
- Post-fabrication polishing: For critical cosmetic parts, you may want to invest in additional processes like polishing or brushing to minimize visible surface imperfections.
- Use protective coatings: For parts that will be exposed to rough conditions or handling, consider adding a protective coating, such as anodizing, to enhance surface durability and prevent scratches.
3. Distortion and Warping
Distortion and warping are particularly common when working with thinner aluminum sheets. These issues can occur during welding or heat treatment due to uneven heating and cooling, causing the metal to expand or contract in unpredictable ways.
How to Overcome It:
- Controlled heating: To reduce warping during welding, preheat the aluminum and use controlled heat settings. This helps to minimize thermal gradients that can cause distortion.
- Strategic clamping: Using proper clamping techniques during welding or fabrication can help ensure the material stays in place and resists warping.
- Thin sheet considerations: For thinner aluminum sheets, consider using methods that minimize heat input, such as laser cutting or waterjet cutting, to avoid warping.
4. Inconsistent Welds and Weak Joints
Aluminum alloys are known for their high weldability, but they can also pose challenges such as inconsistent welds and weak joints, particularly when working with alloys like 7075, which has poor weldability.
How to Overcome It:
- Select the right filler material: When welding, choose a filler metal that matches or is compatible with the base material to avoid weak or brittle joints.
- Preheat the material: Preheating the aluminum before welding can help minimize the risk of cracking and ensure a stronger, more consistent weld.
- Post-weld treatment: After welding, heat treatments like stress-relieving can help eliminate residual stresses and improve the overall strength of the welded joints.
5. Corrosion and Oxidation
Aluminum alloys are generally resistant to corrosion, but they can still suffer from oxidation and pitting, especially when exposed to harsh environments such as saltwater. This is particularly important for marine applications.
How to Overcome It:
- Anodizing: Anodizing aluminum creates a protective oxide layer that increases resistance to corrosion and enhances surface durability.
- Coatings and Paints: Applying corrosion-resistant coatings or paints is another effective way to protect aluminum parts in harsh environments.
- Material Selection: For parts exposed to extreme conditions (e.g., marine applications), consider using alloys like 5052-H32, which offer superior corrosion resistance compared to other alloys like 6061.
6. Difficult Machining and Tool Wear
While aluminum alloys like 6061-T6 are relatively easy to machine, certain grades can present challenges in terms of tool wear and machining precision, especially when working with harder materials. Learn more about Aluminum Machining from our sister company, Approved Machining.
How to Overcome It:
- Proper tool selection: Use high-quality, sharp tools that are designed for aluminum machining to reduce tool wear and improve the precision of your cuts.
- Lubrication: Use cutting fluids or lubricants during machining to reduce heat buildup, prolong tool life, and improve surface finish.
- Optimal machining parameters: Adjust machining speeds and feeds based on the material and the complexity of the part to optimize the machining process and reduce wear.
When a material swap isn’t possible…
When you need your parts formed with 6061-T6 aluminum, Approved Sheet Metal can help. Contact us to discuss your unique needs, learn how we’ll approach your project, and review any major concerns. Whenever possible, we’ll do whatever we can to get you the part you need made just the way you need it.
Get a quote for your next custom aluminum fabrication project.
5052-H32 Versus 6061-T6 for Sheet Metal Fabrication FAQ
6061-T6 aluminum is strong and suitable for machining but prone to cracking when formed to 90 degrees or beyond. In contrast, 5052-H32 aluminum, while less expensive and not heat-treated, excels in forming processes due to its high fatigue strength and elasticity.
5052-H32 offers better formability without the risk of cracking during fabrication, making it an ideal choice for parts requiring tight radii or extensive forming. Additionally, its cost-effectiveness at approximately $2 less per pound than 6061 aluminum adds to its appeal for fabricated parts.
For 6061-T6, its strength and machinability are notable, but potential cracking, cosmetic issues, and the need for larger bend radii are crucial considerations. Conversely, 5052-H32's formability, smoother surface finishes, and cost-effectiveness make it a preferable choice for fabricated parts.
6061-T6 finds use in aerospace, bridges, transportation, and structural applications due to its strength, while 5052-H32 is favored for panels, enclosures, marine equipment, and medical devices where forming requirements are critical.
In cases where 6061-T6 is specified but tight radii or extensive forming is necessary, it's advisable to discuss a material swap to 5052-H32 with the fabricator. Approved Sheet Metal typically recommends this change to ensure better quality and prevent potential complications during fabrication.